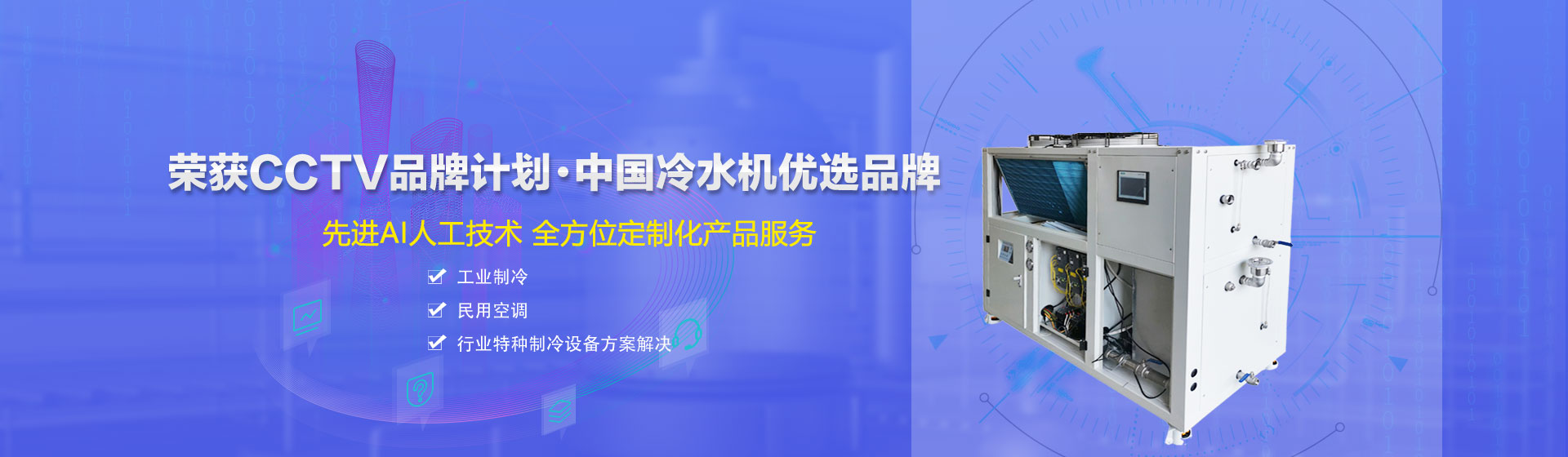
-
What are the key design points of the mold for the mold temperature machine
The business strategy of using mold temperature machines to save manpower, improve quality, and reduce costs is urgent. The use of mold temperature machines can reduce the preheating time of molds, improve the surface quality of finished products, and enable fully automated production. Improving the lifespan of molds is a necessary means to enhance productivity. Mold temperature machines are widely used in various industries such as plastic molding, die-casting of light guide plates, rubber tires, rollers, chemical reaction vessels, adhesives, and mixing.
1. Flat products should not be fed in the middle to prevent bending and deformation.
2. Generally, STP is located directly below RP.
3. When the mold seat is large, the spacing between STPs is 150-200mm.
4. The screw spacing for locking the upper and lower ejector plates is 150-200mm.
5. When there is a needle under the slider or a diagonal tip that breaks, the upper and lower ejection plates should be equipped with a forced return mechanism.
6. The draft angle of the finished product is based on the reduction of material.
7. When designing waterways, try not to use water pipes directly connected to the mold core, but instead use a mold inlet pipe to repair the "O" RING connection mold core.
8. SP should try to increase its diameter and arrange it below the projected area of the finished product.
9. Three principles of cooling water circuit: A Rapid cooling, B Uniform mold temperature, C Easy to process.
10. The distance between the slanted tip and the center of the mold should be rounded off.
11. The KO hole is eccentric with the eccentricity of the injection port liner, and the maximum inclination angle of the injection port liner shall not exceed 15% d.
12. For the two-piece half mold, the separation stroke between the upper fixed plate and the female template needs to be controlled by a mechanism. LP on the male template must have an injection guide liner, and generally requires an LK shutter.
13. The general method for dealing with inner hooks is to use slanted tips, inner sliders, and stripping plates (pushing out the middle plate). The pushing out tip should be avoided as much as possible under the slider to avoid collision or interference.
14. Generally, the mold core exceeds the contour of the finished product by 20-30mm and should be rounded off from the center of the mold. The template should be 20-30mm away from the mold core frame. If there is a slider, the template should be enlarged, and special attention should be paid to avoiding interference with the return pin.
15. The placement of support columns (SP) and the spacing between foot pads should be kept as equal as possible to maintain the balance of their molds.
Refrigeration Encyclopedia