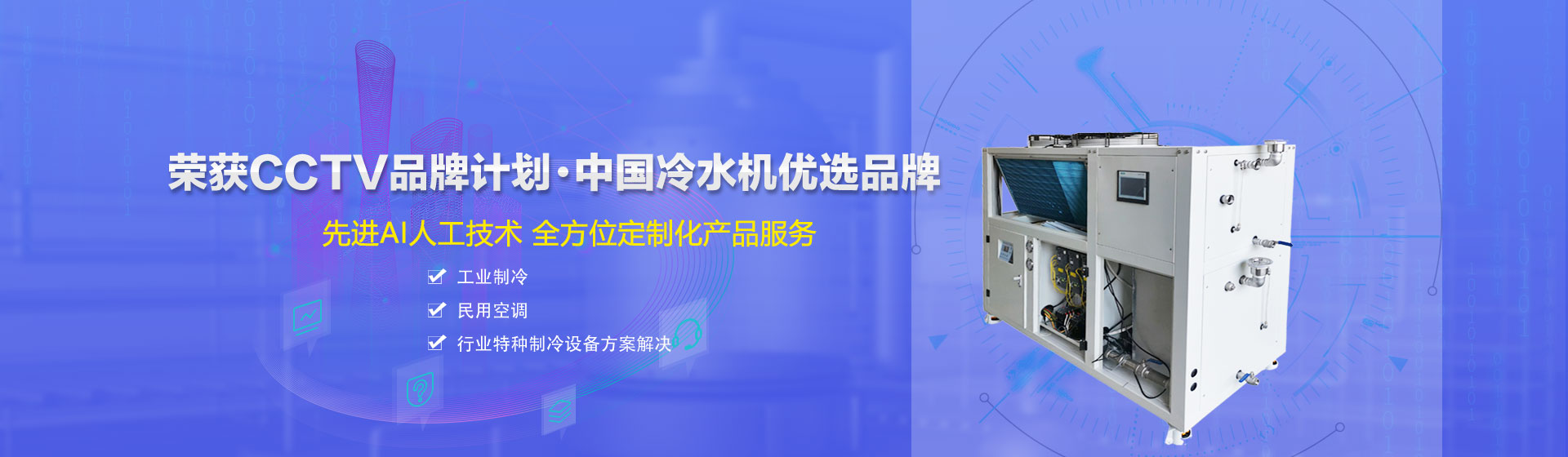
-
What are the applications of chillers in injection molding
1. Application of chiller in plastic molds
The plastic pellets are melted by heating and injected into the mold. After solidification, the mold is opened and the molded plastic workpiece is ejected. In the continuous production process, it is necessary to cool the mold to shorten the plastic solidification time, improve the dimensional accuracy, molding quality, and surface quality of the workpiece.
Temperature requirement for frozen water: 6-18 ℃
Temperature difference requirement for frozen water: ± 2K or ± 0.5K
The cooling capacity of the chiller unit is related to the injection molding volume of the injection molding machine, and the larger the injection molding volume, the greater the required cooling capacity.
2. Application of chillers in injection molding machines
Injection molding machines are usually labeled as "tons" of clamping force, which requires converting "tons" to "Anshi". However, "tons" and "Anshi" do not correspond one-to-one, and the following comparison table is only a general conversion relationship with some deviation.
(1) Extrusion molding
Extruded pipes, cable trays, cables, and various plastic profiles.
After heating and melting the raw materials through the mold, they are cooled in a freezing water bath, and the water temperature in the freezing water bath must be kept constant.
Due to high production speed and the need for large cooling units.
If the existing frozen water tank is large enough, the unit may not be equipped with a water tank.
(2) Blow bottle
We mainly produce various types of mineral water bottles and soda bottles.
Compressed air drying - blowing bottles requires clean and dry compressed air, and the use of frozen water provided by industrial chillers as a cold source can remove moisture from the compressed air.
Mold cooling - electroplating cold water machine can accurately control mold temperature, improve product quality, and increase production efficiency
Compressed air drying and mold cooling can use the same chiller as the cold source
(3) Thermoplastic molding
It is very important to maintain a constant temperature during the extrusion molding of plastic by a mold heated at a constant frequency. The temperature difference range of the chilled water is required to be very high, so a proportional chilled water valve is needed to accurately adjust the temperature.
Refrigeration Encyclopedia