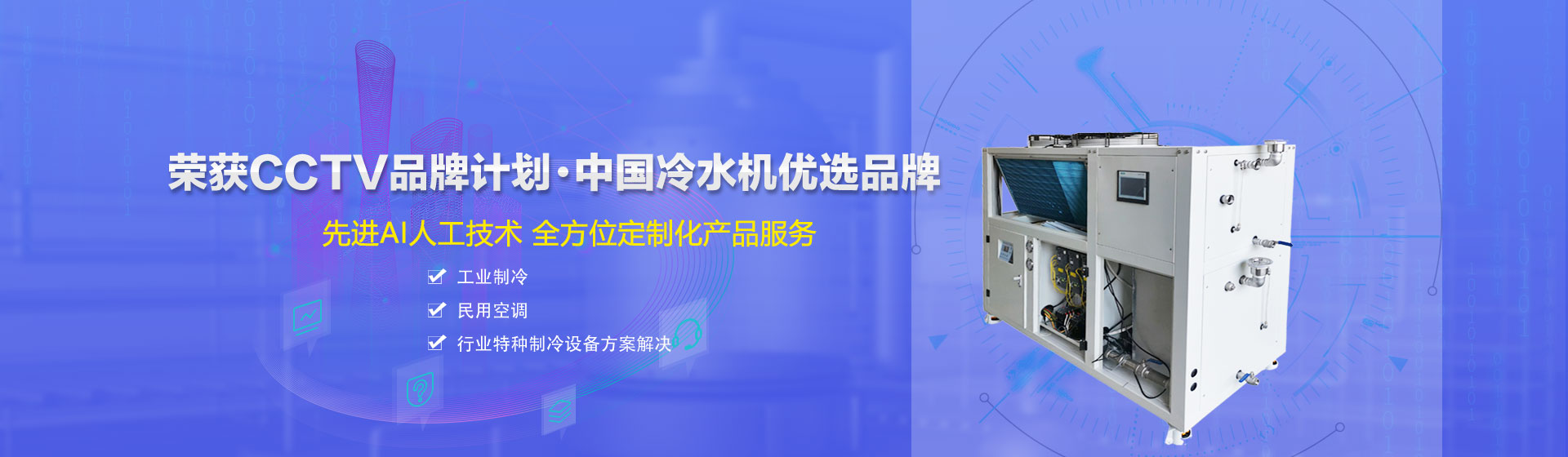
-
Application of screw chillers in the reactor industry
1、 How to solve the problem of high jacket temperature in the reaction kettle, using a screw chiller to explain:
Screw chillers are divided into air-cooled screw chillers and water-cooled screw chillers. For high-power screw chillers, many users choose to make them into multi cycle refrigeration systems. In actual operation, the required refrigeration system can be selected according to production needs.
2、 How to solve the problem of high jacket temperature in the reaction kettle, using the principle of screw chiller:
The screw type chiller is named after its key component - the compressor, which uses a screw type. The unit is powered by a gas refrigerant in the state of the evaporator; After adiabatic compression by the compressor, it becomes a high temperature and high pressure state. The compressed gas refrigerant is cooled and condensed under equal pressure in the condenser, and then transformed into liquid refrigerant after condensation. It is then expanded to low pressure through a throttle valve and becomes a gas-liquid mixture. The liquid refrigerant under low temperature and pressure absorbs the heat of the cooled substance in the evaporator and transforms back into a gaseous refrigerant. The gaseous refrigerant enters the compressor again through the pipeline and starts a new cycle. These are the four processes of the refrigeration cycle. This is also the main working principle of screw chillers. The application of screw chillers. Compared with vortex chillers, screw chillers have relatively higher power and are mainly used in central air conditioning systems or large-scale industrial refrigeration. Classification of screw chillers: According to different heat dissipation methods, screw chillers can be divided into water-cooled screw chillers and air-cooled screw chillers. Product selection points: 1.2. The selection of chiller units should be considered according to the cooling load and purpose. For refrigeration systems that operate under low load conditions for a long time, it is advisable to use multi head piston compressor units or screw compressor units for easy adjustment and energy saving. When selecting a chiller unit, priority should be given to units with higher performance coefficient values. According to data statistics, the operating time of a general chiller unit at 100% load throughout the year accounts for less than 1/4 of the total operating time. The proportion of operating time at 100%, 75%, 50%, and 25% load within the total operating time is approximately 2.3%, 41.5%, 46.1%, and 10.1%. Therefore, when selecting chillers, priority should be given to models with relatively flat efficiency curves. At the same time, the adjustment range of the load of the chiller unit should be considered when designing and selecting. The multi head screw chiller unit has excellent partial load performance and can be selected according to actual conditions. When selecting a chiller unit, attention should be paid to the nominal operating conditions. The actual cooling output of a chiller unit is related to the following factors: a) cold water outlet temperature and flow rate; b) The inlet temperature, flow rate, and fouling coefficient of the cooling water. When selecting a chiller unit, attention should be paid to the normal operating range of the unit model, mainly the current limit of the main motor is the current value of the shaft power under nominal operating conditions. 6. In design selection, attention should be paid to: under nominal operating flow conditions, the outlet temperature of cold water should not exceed 15 ℃, and the outdoor dry bulb temperature of air-cooled units should not exceed 43 ℃. If it is necessary to exceed the above range, it should be understood whether the usage range of the compressor is allowed and whether the power of the main motor is sufficient.
Refrigeration Encyclopedia