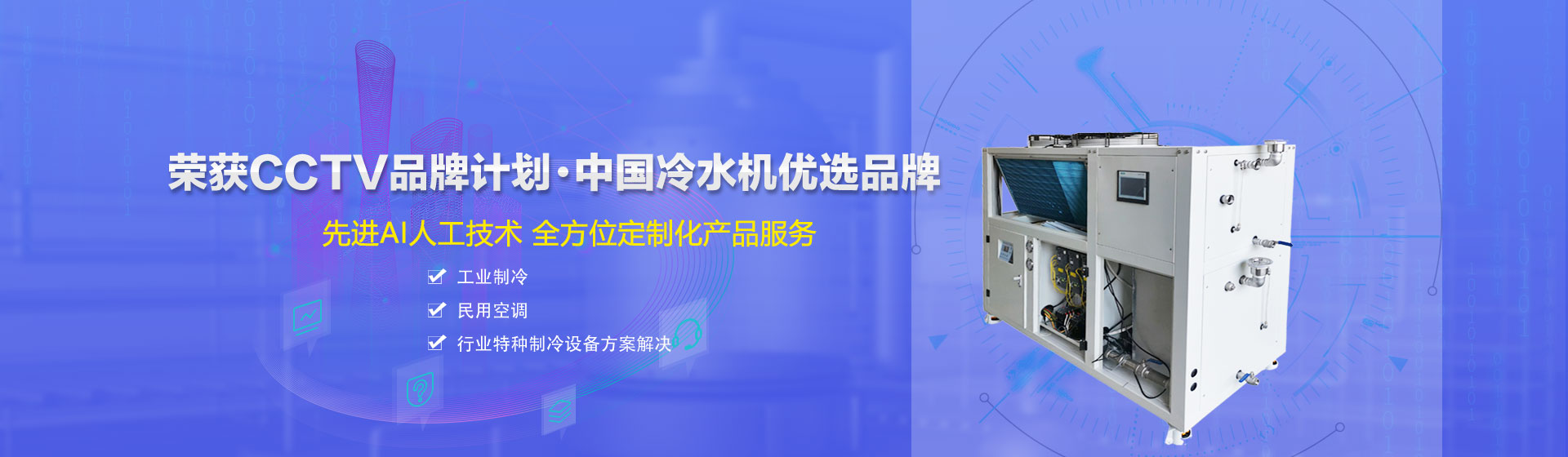
-
What are the main components of a chiller unit?
The basic structure of a chiller is that the four main components of a refrigeration system are the compressor, evaporator, condenser, and expansion valve. In order to improve the performance of the refrigeration system and achieve better usability, there are usually many auxiliary components such as liquid pipeline solenoid valves, sight glasses, liquid pipeline drying filters, high and low pressure controllers, etc.
Introduction to the main components and equipment of chiller units
1. Compressor of chiller unit
In the chiller system, the compressor is the power source to ensure refrigeration. By using the compressor to increase the pressure of the refrigerant in the system, the refrigerant circulates in the refrigeration system to achieve the purpose of refrigeration. Compressors are classified into three types based on their structure: open type, semi closed type, and fully closed type. Most of our company's chilled water units use fully enclosed compressors for chilled water above 0 ℃.
A fully enclosed refrigeration compressor is a unit formed by a compressor and an electric motor installed in a sealed iron shell. From the appearance, only the suction and exhaust pipe joints of the compressor and the wires of the motor are visible; The compressor casing is divided into upper and lower parts. After the compressor and motor are installed, the upper and lower iron casings are welded together by electric welding. It cannot be disassembled normally, so the machine is reliable to use. In fully enclosed refrigeration compressors, there are also piston compressors and scroll compressors.
The structure of a fully enclosed vortex refrigeration compressor mainly consists of the following components: rotary inlet and outlet valves; Pressure gauge interface; Built in overload protection; Elastic machine base; Crankcase heater; Built in lubricating oil pump.
The biggest advantage of a scroll refrigeration compressor is: 1. Simple structure: the compressor body only requires 2 components (moving plate, fixed plate) to replace 15 components in a piston compressor; 2. Efficiency: The suction gas and the transformation process gas are separated to reduce heat transfer between suction and process, which can improve the efficiency of the compressor. The vortex compression process and transformation process are both very quiet.
2. Condenser of chiller unit
The high-temperature and high-pressure Freon in the refrigeration system enters the condenser after coming out of the compressor, releasing a large amount of heat to the cooling medium and being cooled and liquefied. So, condensers can be divided into two types based on their cooling methods: water-cooled and air-cooled.
(1. Water cooled type
In a water-cooled condenser, the heat released by the refrigerant is carried away by the cooling water. Cooling water can flow through once or be recycled. When using circulating water, a cooling tower or cold water tank is required. Water cooled condensers come in various structural forms such as shell and tube, sleeve, and immersion.
The commonly used condenser for water-cooled chillers is the shell and tube condenser, which is made of steel pipes with a thickness of 5mm or more, treated with rust prevention, and has a pressure resistance of 20Kg/square centimeter. The heat exchange tube adopts high-efficiency seamless copper tube with a pressure resistance of 10 Kg/square centimeter. The two end caps can be interchanged to change the direction of the water pipe. The water pipe process is multi loop, and the capacity of each condenser and compressor is coordinated. Its total thermal conductivity should be able to tolerate a scaling factor of 0.00005 Kcal/h. square centimeter ℃ -1, and the water pressure drop of the condenser should not exceed 6.5 meters
Refrigeration Encyclopedia